on its way to the starting air system, must bypass
through a pressure-reducing valve, which reduces
the higher pressure to the operating pressure
required to start a particular engine.
A relief valve is installed in the line between
the reducing valve and the starting system. The
relief valve is normally set to open at 12 percent
above the required starting air pressure. If the air
pressure leaving the reducing valve is too high,
the relief valve will protect the system by releasing
air in excess of a preset value and permit air only
at safe pressure to reach the starting system of
the engine.
START AIR MOTOR SYSTEM. Some
engines, usually gas turbine types, are designed
to crank over by starting motors that use
compressed air. Air-starting motors are usually
driven by air pressures varying from 90 to 200 psi.
COMPRESSED AIR ADMISSION SYSTEM.
Most large diesel engines are started when
compressed air is admitted directly into the engine
cylinders. Compressed air at approximately 200
to 300 psi is directed into the cylinders to force
the piston down and thereby, turn the crankshaft
of the engine. This air admission process continues
until the pistons are able to build up sufficient
heat from compression to cause combustion to
start the engine.
GASOLINE ENGINES
The main parts of the gasoline engine are quite
similar to those of the diesel engine. The two
engines differ principally in that the gasoline
engine has a carburetor and an electrical ignition
system.
The induction system of a gasoline engine
draws gasoline from the fuel tank and air from
the atmosphere, mixes them, and delivers the
mixture to the cylinders. The induction system
consists of the fuel tank, the fuel pump, the
carburetor, and the necessary fuel lines and air
passages. Flexible tubing carries the fuel from the
tank to the carburetor, while the intake manifold
carries the fuel-air mixture from there to the
individual cylinders. The fuel-air mixture is ignited
by an electric spark.
The carburetor is a device used to send a fine
spray of fuel into a moving stream of air as it
moves to the intake valves of the cylinders. The
spray is swept along, vaporized, and mixed with
the moving air. The carburetor is designed to
maintain the same mixture ratio over a wide range
of engine speeds. The mixture ratio is the number
of pounds of air mixed with each pound of
gasoline vapor. A rich mixture is one in which the
percentage of gasoline vapor is high, while a lean
mixture contains a low percentage of gasoline
vapor.
The electrical ignition system is designed to
deliver a spark in the combustion chamber of each
cylinder at a specific point in that cylinders
cycle of operation. A typical ignition system
includes a storage battery, an ignition coil, breaker
points, a condenser, a distributor, a spark plug
in each cylinder, a switch, and the necessary
wiring.
There are two distinct circuits in the ignition
systemthe primary and the secondary. The
primary circuit carries a low-voltage current. The
secondary circuit is high voltage. The battery, the
ignition switch, the ignition coil, and the breaker
points are connected in the primary circuit. The
secondary circuit, also connected to the ignition
coil, includes the distributor and the spark plugs.
The storage battery is usually 6, 12, or 24 volts.
One terminal is grounded to the engine frame,
while the other is connected to the ignition system.
The ignition coil, in many respects, is similar
to an electromagnet. It consists of an iron core
surrounded by primary and secondary coils. The
primary coil is made up of a few turns of heavy
wire, while the secondary coil has a great many
turns of fine wire. In both coils, the wire is
insulated and the coils are entirely separate from
each other.
The breaker points form a mechanical switch
connected to the primary circuit. They are opened
by a cam that is timed to break the circuit at the
exact instant that each cylinder is due to fire. A
condenser is connected across the breaker points
to prevent arcing and to provide a better high-
voltage spark.
The distributor, connected to the secondary
or high-voltage circuit, serves as a selector switch
that channels electric current to the individual
cylinders. Although the breaker points are
connected in the primary circuit, they are often
located in the distributor case. The same drive
shaft operates both the breaker points and the
distributor.
The spark plugs, which extend into the
combustion chambers of the cylinders, are
connected by heavily insulated wires to the
distributor. A spark plug consists essentially of
a metal shell that screws into the spark plug hole
in the cylinder, a center electrode embedded in
7-13
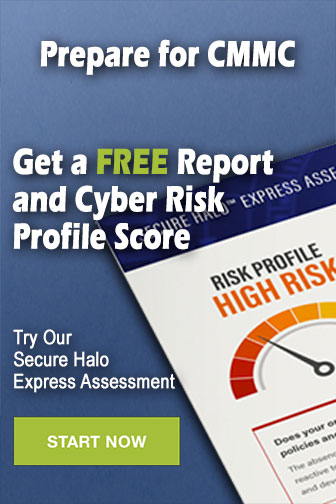