Trouble Log
Trouble reports and logs are usually filled out each
time an equipment trouble is detected. They are
generated locally and are a great help in filling out 3-M
documents because they tell you what equipment is
affected, the nature of the trouble, and the time of the
failure. After you have corrected the trouble, you
should make an entry in the report or log stating that the
correction has been completed, including the date of
completion and your signature.
Sometimes equipment belonging to someone else
but located in your work center breaks. An example of
this might be a bad phone circuit or a blown fuse. In
these cases you should call the respective trouble call
desk. This might be Damage Control Central (or
equivalent) or the Combat Systems Officer of the
Watch (CSOOW). The trouble call desk will give you a
number that represents your call and the associated
fault. Each trouble desk has its own log and will record
your trouble call in it. Make sure that you put this
number in your work centers trouble log to ensure that
you also have a record of the fault. You can use a blank
book, binder, folder or whatever you think will get the
job done in keeping accurate records of these types of
faults. Its a good idea to have the person correcting the
fault sign or initial the log after the fault has been
corrected. This will give you an accurate history of
your work centers non-equipment related casualties.
Other locally generated logs that may be used are
test equipment checkout logs (to track test equipment
on loan to other divisions), consumable usage logs (to
track the use of consumable supplies), and tool
a c c o u n t a b i l i t y l o g s ( t o t r a c k t o o l s i s s u e d t o
individuals).
Supply Log
Your work center uses the supply log to list and
keep track of parts you have ordered in order to support
equipment maintenance or repair. Normally the person
assigned as Repair Parts Petty Officer (RPPO) will
make entries and update the supply log as required.
This log is kept in your work center with other
important records. You can either use a pre-printed
form that is already divided into rows and columns
(ordered through your supply system) or create your
own record. An important thing to remember is to be
consistent in making entries when you order, receive or
update parts for your equipment. This will ensure that
you get parts support in a timely manner and that you
dont waste time and money because of careless supply
log maintenance. Your supply department will give
you specific directions on keeping a good supply log
and will direct you in complying with your ships
i n s t r u c t i o n s . T h e r e a r e s p e c i f i c p e r s o n n e l
qualifications standards for repair parts petty officer
that will guide you in preparing a supply log and in
performing the duties of a good repair parts petty
officer. Check with your divisional chain of command
or the supply department for the latest requirements
and training for repair parts petty officer.
Preventative Maintenance System (PMS)
Accountability Log
The PMS accountability log is used to keep track
of maintenance performed on a system or piece of
equipment within the last 13 weeks. It documents the
maintenance done on equipment according to the
maintenance requirement card (MRC), the actual date
maintenance was completed, and the signature of the
person who did the actual maintenance. This is a
required log in your work center and is subject to
r o u t i n e i n s p e c t i o n . I n s p e c t i o n o f t h e P M S
accountability log is usually done on a weekly basis,
but can be done at any time. For specific instructions
for your work center, check your ships instructions
and the 3-M manual.
Tag-Out Log
The tag-out log documents the issuing of safety
tags (normally danger tags) required for maintenance
or repair of equipment. This log is commonly referred
to as a laminated tag-out log.
This program is
authorized by the commanding officer. At the
discretion of the commanding officer, certain work
centers are allowed to use laminated danger tags. The
ship will have a local instruction that details all
r e q u i r e m e n t s f o r t h i s p r o g r a m a n d w h a t t h e
commanding officer expects of work centers that are
allowed the privilege of using laminated danger tags.
Laminated danger tags are numerically serialized
danger tags that are laminated for use in routine,
periodic maintenance. They are filled out with grease
pencil and subject to the same type of signature
requirements and logging as any danger tag.
Laminated tags can only be used for one working day
and may not be used for maintenance or repair that
extends beyond the normal work day. If a danger tag is
needed for more than one working day, the normal tag
out procedures for the department apply. Laminated
tags are audited on a daily basis by the work center
supervisor and on a weekly basis by the division
1-3
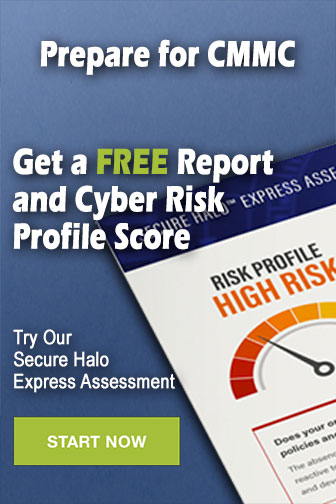