in the supply pressure (as long as the supply
pressure is at least as high as the reduced pressure
desired) and regardless of the amount of reduced
pressure fluid that is used.
Various designs of pressure-reducing valves
are in use. Two of the types most commonly
found on gas turbine ships are the spring-loaded
reducing valve (already discussed) and the air-pilot
operated diaphragm reducing valve.
Air-pilot operated diaphragm control valves
are used extensively on naval ships. The valves
and pilots are available in several designs to
meet different requirements. They may be
used to reduce pressure, to increase pressure,
as unloading valves, or to provide continuous
regulation of pressure. Valves and pilots of
very similar design can also be used for
other services, such as liquid-level control and
temperature control.
The air-operated control pilot may be
either direct acting or reverse acting. A direct-
acting, air-operated control pilot is shown in
figure 9-26. In this type of pilot, the con-
trolled pressurethat is, the pressure from
the discharge side of the diaphragm control
valveacts on top of a diaphragm in the
control pilot. This pressure is balanced by
the pressure exerted by the pilot adjusting
spring.
If the controlled pressure increases
and overcomes the pressure exerted by the
pilot adjusting spring, the pilot valve stem
is forced downward. This action causes the
pilot valve to open, thereby increasing the
amount of operating air pressure going from
the pilot to the diaphragm control valve.
A reverse-acting pilot has a lever that re-
verses the pilot action. In a reverse-acting
pilot, therefore,
an increase in controlled
pressure produces a decrease in operating air
pressure.
Figure 9-26.Air-operated control pilot.
9-18
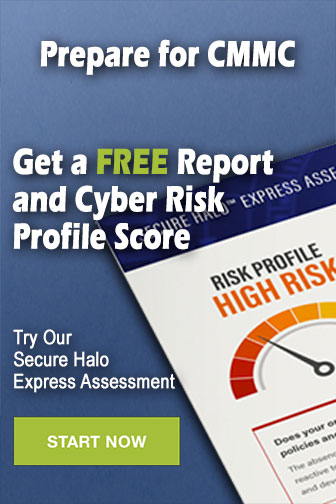