Disk Platters
Head Crash Effects
The size of the disks platters varies, depending on
intended use, capacity, and speed. Sizes of the disk
platters commonly used are 5.25-inch, 3.5-inch and
2-inch.
Fixed disk systems may contain from 1 to 11
platters, depending on size and capacity. The number
of platters in a drive is limited by the size of the drive.
Half-height 5.25- and 3.5-inch drives contain a
maximum of eight platters. Full-height drives are
currently limited to 11 platters. Since the platters are
sealed in the HDA, all of the surfaces are used for data
storage.
Platters are made of aluminum alloy metal coated
with a magnetic material (medium). The two most
common media for fixed disk platters are iron oxide and
thin film.
IRON OXIDE COATED PLATTERS. Iron
oxide platters are found in many older low-density
drives. The oxide is applied to the platter, then cured
and polished. The iron oxide is generally applied to a
thickness of 30 millionths of an inch. After the platter
is polished, a protective lubricant is applied to help
prevent damage caused by head crashes.
THIN FILM COATED PLATTERS. Thin film
coated platters can hold much greater data densities
because the magnetic coating is much thinner and more
perfectly formed than the iron oxide coating. Two
processes, plating and sputtering, are used to
manufacture thin film disks.
Platting Platting is a process in which the
medium is applied to the disk using an electroplating
mechanism. The final layer is a cobalt alloy of
approximately 3 millionths of an inch.
Sputtering Sputtering is a process in which the
cobalt alloy is applied in a near vacuum. The magnetic
material, as thin as 2 millionths of an inch, is deposited
on the disk in much the same way metallic films are
applied to silicon chips in the creation of
semiconductors. A hard carbon coating is then applied
to protect the disk.
The result, on both plated and sputtered disks, is an
extremely thin and hard medium on the disk. The hard
surface increases the probability that the disk will
survive a high-speed head crash with little or no
damage.
10-24
A head crash occurs whenever the heads come in
contact with the disks surface. Severe damage can
occur if the heads crash with the disk spinning at full
speed. The heads can scratch the oxide material or the
heads themselves can be damaged. Whenever the disk
is powered down, there is a minor head crash as the disk
slows down.
Many fixed disks have a designated
landing zone for the heads, but you have to position the
heads in this landing zone. To do this you should run a
program designed to park the heads in this landing zone
before removing power.
The thinner medium requires a smaller space on the
disk to store data. Also the heads can fly closer to the
disk, further reducing the space and magnetic field
strength required to accurately store data and increase
densities.
Read/Write Heads
The read/write heads used infixed disk systems are
very similar to the read/write heads on the disk memory
set. There is one head for each disk surface. These
heads are joined to the head actuator and move in unison
across the disk. There are currently two types of heads
in use: the composite ferrite head and the thin film
head.
COMPOSITE FERRITE HEAD. The
composite ferrite head is the traditional type of head
used in magnetic recording. It consists of an iron oxide
core wrapped with electromagnetic coils. To write data
on the disk, an electric current is passed through the
coils and a magnetic field is induced on the ferrous
material of the disk surface. Changing the direction of
current flow through the heads coil will result in a
reversal of the magnetic field on the disk.
THIN FILM HEAD. The thin film head is
actually a specialized integrated circuit chip. The head
has a precise U-shaped groove in its bottom to allow the
right amount of air pressure for the head to fly at the
proper height. This lightweight head flies closer to the
disk than the composite ferrite heads.
A thin film heads flying height can be as little as 5
millionths of an inch above the disk. The closeness of
the head to the platter increases the signal-to-noise ratio,
which increases the accuracy of the disk system.
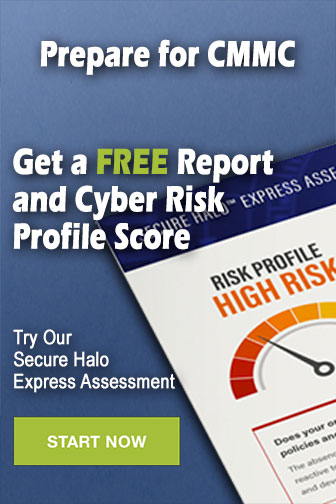