sions are usually the same for differently rated regu-
lators.
Normally used with a pressure-regulating valve,
the nominal flow rate of the equipment-flow regu-
lator, shown in figure 2-13, can be from 1/2 to more
than 12 gallons per minute. However, this type of
regulator can deteriorate over time, with the insert
becoming distorted and causing a reduction in water
flow. With a drill index set, you can use the back of a
drill bit to measure the hole size and compare it to a
known good constant-flow regulator or to the equip-
ment manual. Do not drill out the insert to restore it to
the proper size, because it will become distorted, thus
preventing the insert from regulating the distilled-
water flow.
Figure 2-13.Equipment-flow regulator.
The pressure-regulating valve is used to regulate
a major section of the cooling system, whereas the
flow regulator is normally used to regulate an individ-
ual feeder line to an individual component or cabinet.
The pressure-regulating valve usually has a pressure-
relief valve downstream from it to protect the equip-
ment from becoming overpressurized. If a failure
occurs in the pressure-regulating valve, the pressure-
relief valve will keep the water pressure at a safe level
to prevent equipment damage.
In a typical pressure-regulating valve, when a drop
in downstream (outlet) pressure occurs, the pressure
2-16
in the diaphragm chamber is lowered concurrently.
The downstream side of the valve is connected to the
diaphragm chamber through a narrow opening along
the periphery of the piston.
The spring is allowed to force the diaphragm
downward, releasing the tension on the rocker arm,
and the inlet pressure opens the valve. The outlet pres-
sure increases to the preset level, and the static control
chamber pressure balances the valve spring to main-
tain a regulated downstream pressure to the served
equipment.
You should take certain precautions with this type
of valve. For example, ensure that the locknut is loose
before you adjust the adjusting screw; otherwise, you
could strip the threads of the brass spring chamber. If
water starts leaking out of the vent, have the valve
serviced for a leaking diaphragm before it ruptures.
Never plug or paint over the vent to inhibit its opera-
tion.
If you remove a flow regulator or a pressure regu-
lator, make certain that you reinstall it correctly, as it
can be installed backwards. Look for an arrow for the
direction of the flow or the inlet and outlet stamped on
the body of the device. Pipe-joint sealant should be
used only on the male pipe threads and not closer than
one thread to the open end to seal the device. Figure
2-14 shows a pressure regulator.
Figure 2-14.Pressure regulator.
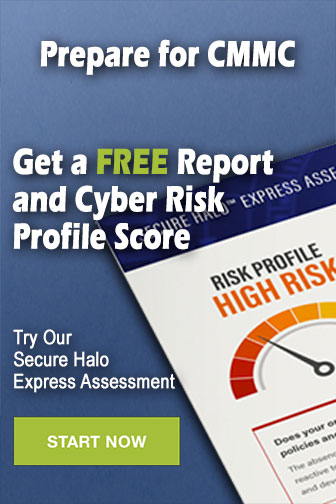