Equipment Benchmarks
Each equipment with an alignment telescope has
a benchmark that can be sighted through the tele-
scope. Equipment benchmarks are installed at any
convenient location that is visible through the equip-
ment telescope. These benchmarks are used through-
out the life of the ship to verify that the alignment is
still within tolerance.
ESTABLISHMENT OF PARALLELISM
The third major alignment step is the establish-
ment of parallelism between the RPPs of all equip-
ment in the combat system. The degree of parallelism
required is based on the design and manufacturing
criteria, the operational environment, and the require-
ments of the various operational modes. The steps
necessary to achieve the degree of parallelism re-
quired are inclination verification, foundation ma-
chining, and interequipment leveling.
Inclination Verification
Inclination verification consists of measurements
of the tilt between two RPPs. The amount by which
one RPP is tilted with respect to another RPP is ex-
pressed as the angle of inclination between the planes
and the bearing where this inclination occurs. The tilt
of the RPP is usually determined by the two-clino-
meter method or the horizon-check method.
Foundation Machining
Foundation machining pertains to the physical
processes required to attain a specified degree of
parallelism and is performed by a support activity.
Physical processes may involve using milling ma-
chines or welding premachined surfaces in place.
Machining is accomplished with the ship afloat and
loaded to simulate the fill-load-deflection curve and
the strains of major concentrated loads. The ship is
kept in the specified loaded condition for a sufficient
period of time (48 hours) before the start of machining
operations to allow ship structural members to adjust
to the load. Strict adherence to normal shipyard tech-
niques of machining during periods of minimum tem-
perature changes is observed.
Interequipment Leveling
Interequipment leveling is achieved by leveling
rings, shims, adjusting screws, or software compensa-
tion. Leveling capabilities are used to achieve the RPI
tolerances imposed by the minimum acceptable re-
quirements or the various operational modes of the
combat system. Where leveling capabilities are not
provided, RPI tolerances are achieved through foun-
dation machining. In cases where foundation machin-
ing is initially used to meet these tolerances, RPI
compensation through computer software changes
may be introduced, if necessary.
PERFORMANCE OF FIRE-CONTROL
RADAR RADIO-FREQUENCY
OPTICAL ALIGNMENT
The fourth major alignment step is the verification
of fire-control radar radio-frequency (RF) optical
alignment (collimation). During initial installation, the
RF optical alignment is established and the optics are
secured in place. During subsequent alignment
checks, the radar antennas or the optics, as applicable,
are adjusted to correct any alignment error between
the optical axis and the RF axis. When the radar is
tracking, the RF axis is the reference used for target
location. RF optical alignment is an equipment-level
test and is performed on a certified shore tower facil-
ity or, in the case of some radars, may be performed
while tracking a target.
ESTABLISHMENT OF TRAIN AND
ELEVATION ZERO ALIGNMENT
The fifth major alignment step is the train and ele-
vation zero alignment. This alignment, performed by
the ships force or a support activity, is conducted to
ensure that all combat systems equipment points to
the same point in space when so directed.
3-14
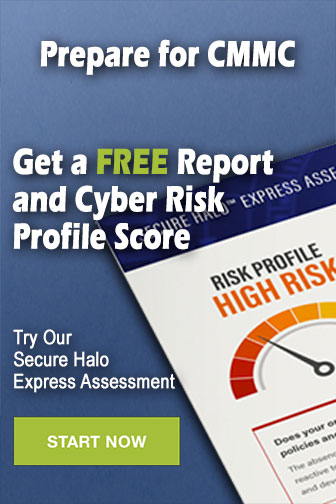