1. LOGIC DIAGRAMS: Logic diagrams in-
clude troubleshooting logic charts (TLCs), fault logic
diagrams (FLDs), fault isolation pyramid charts, and
fault reference tables. The TLCs and the FLDs pro-
vide a simple yes-or-no, question-and-answer ap-
proach to fault isolation. They are generally based on
either a ladder method or a bracket-and-halving fault-
isolation technique.
Ladder Method: The function is approached
from its initiation or termination point and, in succes-
sive steps, is checked to the other end.
Bracket-and-Halving Fault-Isolation Tech-
nique: The function is checked at its midpoint, then at
the midpoint of the half containing the fault, etc., until
it is isolated.
Pyramid charts take an output or terminal func-
tion (output, indicator, etc.) and break it down into its
major subfunctions, which are individually checked
until the fault is isolated. Fault reference charts gen-
erally relate symptoms to specific faults.
2. FUNCTIONAL FLOW DIAGRAMS: Func-
tional flow diagrams include system functional dia-
grams, signal-flow diagrams, schematic diagrams, and
relay-ladder diagrams. These are frequently used in
isolating a fault that was not anticipated by the fault
logic material provided.
In general, fault logic procedures are used more
rapidly by inexperienced technicians than fictional
diagrams in isolating a specific fault. When used with
flow diagrams, fault logic procedures provide a means
of teaching new or inexperienced personnel effective
fault-isolation techniques. A fictional understanding
gained through the use of maintenance documents is
necessary for the development of experienced tech-
nicians. Experienced technicians frequently isolate
specific faults addressed in fault logic procedures
faster without referring to procedures. Their experi-
ence is essential in isolating problems that have not
been anticipated by logic procedures.
Numerous approaches are possible in the applica-
tion of fault-isolation procedures. The fact that most
casualties occur within an equipment and are cor-
rected by troubleshooting on an equipment-level basis
leads to the tendency to troubleshoot all casualties on
an equipment-level basis. It is to be expected that each
technician might rely more heavily on certain trouble-
shooting aids and procedures than others. Few hard-
and-fast rules apply to all troubleshooting situations,
but one rule that should always be foremost is to de-
termine the origin of a fault as precisely as possible.
System interrelationship is such that many casual-
ties can be reflected in several areas as improper op-
eration or fault indications. If each area of each
equipment that does not function properly is checked
separately, the equipment downtime and correspond-
ing man-hour use can rapidly increase. On the other
hand, familiarity with system reference materials,
system fictional diagrams, and fault-isolation proce-
dures can lead logically and expeditiously to the spe-
cific area of the fault.
All system fault isolation is interrelated. Its
effective use depends on knowing what materials are
available, how they are interrelated, and how to cross-
-reference between materials. The isolation materials
that you will use in fault isolation are the system fault
indicator director, the system function directory, the
system functional diagram, the fault analysis matrix,
a sample troubleshooting problem, and the equipment
troubleshooting documentation.
System Fault Indicator Directory
The system fault indicator directory (FID) facili-
tates entry into the documentation required for
troubleshooting a fault disclosed by a specific indica-
tor during normal operation. A typical FID is shown
in table 1-3. The material in this FID is grouped by
system and further divided alphabetically by equip-
ment, panel, and indicator. A complete listing of indi-
cators is included.
1-11
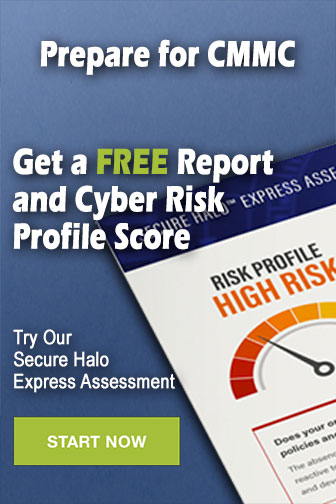