(dogleg) is the preferred configuration; however,
where space and piping arrangement prohibit the
use of the L configuration, a 180° or U
configuration may be used. The 90° L and
180° U configurations are shown as sketches
A and B of figure 9-50.
A configuration that uses a single length of
hose bent to about 90° is approved where the hose
does not bend below its specified minimum
bending radius when the equipment moves to the
maximum limits allowed by its mounts (view A
of fig. 9-51). The straight single hose configura-
tion and the 180° single hose bend (view B of fig.
9-51) are also approved for use where the hose
size is less than 1 inch ID.
Flexible connections that use rubber hose are
not used in systems where the maximum
continuous operating temperature is in excess of
200°F.
Hose Identification
Hose is identified by the manufacturers part
number and the size or dash number. The dash
number is the nominal hose inside diameter in
sixteenths of an inch. Hose built to military
specification (MILSPEC) requirements have the
number of the specification and, where applicable,
the class of hose, the quarter and year of manu-
facture, and the manufacturers trademark. This
information is molded or otherwise permanently
repeated periodically on the hose cover (sometimes
referred to as the lay line marking). Other
information permanently marked on the hose
cover is the manufacturers code and the date of
manufacture. For interpretations of commercial
lay line markings, refer to the appropriate
manufacturers catalog or manual.
Fitting Identification
Use special care in identifying hose fittings
because their designation is more complex than
hose. A fitting suitable for connecting to a given
hose size can end in more than one size and type
of connection to the piping. A fitting, therefore,
must be identified by the manufacturers part
number, the size of the end connection that joins
the piping system, and the dash size to show the
size hose to which it makes up. For interpreta-
tion of manufacturer markings, consult the
appropriate manufacturers manual. Fittings
meeting military specification requirements have
the specification number, class of fitting (where
applicable), type, size, and manufacturers
trademark.
A cross index between the manufacturers
designations and military specifications and
information to correctly identify approved hoses
and fittings can be found in Piping Devices,
Flexible Hose Assemblies, volume 1, NAVSEA
S6430-AE-TED-010.
Inspection of Hose and
Fittings Prior To Make-Up
The basic inspection methods for hose and
fittings are listed as follows:
1.
2.
3.
4.
5.
6.
Ensure that the hose and couplings are the
correct ones for the intended use and that
the age of the rubber hose does not exceed
a shelf life of 4 years. Teflon and metal
hose have no limiting shelf life.
Inspect for signs that the hose has been
twisted. Use the hose lay line for a guide
to determine whether or not any twist is
present. If twisted, reject.
Inspect for signs that the hose has been
kinked or bent beyond its minimum bend
radius. If suspect, reject.
Inspect for signs of loose inner liner. If
found, cut the hose to see if this condition
exists throughout the entire length. If
.
suspect, reject.
Visually check the inner liner and outer
rubber cover of the hose for breaks,
hairline cuts, or severe abrasions. If any
suspect areas are found, reject.
Inspect the fittings for defects, such as
cracked nipples and damaged threads.
If suspect, or if defects are found, reject.
Procedures for making up hoses and fittings
can also be found in the NSTM, chapter 505, or
the appropriate manufacturers catalog or
manual, and are not covered here due to the many
types available.
Visual Inspection
After assembling the hose and fittings, visually
inspect the entire configuration to ensure the
following:
1.
2.
The hose inner liner and outer cover is
intact and contains no cuts or harmful
abrasions.
The hose has not been twisted (check the
lay line).
9-34
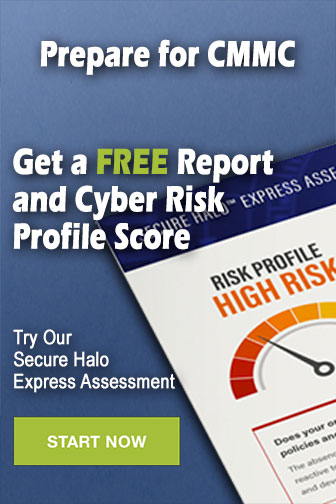