3.
4.
The circumferential chalk line on the hose
next to the coupling has been drawn before
the hydrostatic test.
The internal spring (if installed) is evenly
spaced and flat against the inner liner.
Ensure a gap exists between one of the end
fittings and the end of the spring.
Hydrostatic Test
Upon completion of visual inspection, hydro-
statically shop test the hose assembly with fresh
water. For each style and size of hose, test the
pressure to ensure that it is twice the maximum
allowable pressure shown in chapter 505 of the
NSTM. When you test pressure, hold for not
more than 5 minutes nor less than 60 seconds.
When test pressure is reached, visually inspect the
hose assembly for the following defects:
1. Leaks or signs of weakness
2. Twisting of the hose (this indicates that
some twist existed before pressure was
applied)
3. Slippage of the hose out of the coupling
(a circumferential chalk line can help deter-
mine this)
If any of these defects occur, reject the
assembly.
CAUTION
Do not confuse hose elongation under
pressure with coupling slippage. If the
chalk line returns to near its original
position, no slippage has occurred and the
assembly is satisfactory. If there is any
doubt, perform a second test. If doubt
persists after the second test, reject the
assembly.
Air Test
Hose assemblies intended for gas or air
service must also be tested with air or nitrogen
at 100 psi and the assembly immersed in water.
Random bubbles may appear over the hose and
in the fitting area when the assembly is first
pressurized. Do not construe this as a defect.
However, if the bubbles persist in forming at a
steady rate at any particular point on the hose,
reject the assembly.
Installation of Flexible Hose Assemblies
After completion of tests, proceed as follows:
1.
2.
3.
4.
Install as soon as possible.
Do not leave the hose assembly around on
decks or on docks where they can be sub-
jected to any form of abuse.
Make up hose assemblies as late as
possible during the availability schedule to
minimize the chances of damage while the
ship is being overhauled.
Install plastic dust caps, plugs, or tape ends
to protect threaded areas until the hose
assembly is installed.
When installing flexible base connections,
observe the following requirements:
1.
2.
3.
4.
5.
6.
Ensure each leg of hose is free of twist
between end fittings.
Ensure the fixed piping near the flexible
configuration is properly supported so that
it does not vibrate from the resiliently
mounted equipment.
Ensure the configurations are clear of all
surrounding structures and remain so when
resiliently mounted equipment moves
through its maximum excursion under
shock.
Locate flexible connections as close as
possible to the sound-mounted unit.
Support the free elbow of the configura-
tion with an approved pipe hanger so as
not to sag or otherwise unduly stress or
distort the configuration.
Do not appreciably change the alignment
of the hose configuration between the un-
pressurized and pressurized conditions. If
you do, you could cause misalignment or
improper support at the fixed end.
9-35
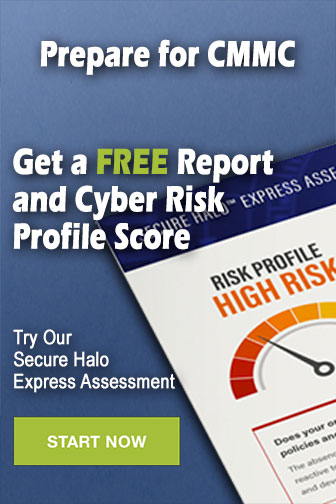