Failure of an O-ring can sometimes begin with
the removal of an old O-ring. If you incorrectly
remove an O-ring with pointed or sharp tools, you
can scratch or dent critical surface finishes that
can result in seal failure.
Before installing a new O-ring, inspect the
sealing surfaces for any abrasions and wipe them
free of any dust, dirt, or other contaminants.
Before installation, inspect the O-ring for any
damage. If faulty, discard it.
When you install the O-ring, lubricate it. In
most cases it is already coated with the system
fluid or petrolatum grease. Do not stretch the
O-ring more than twice its original size during
installation, and do not roll or twist it into
place. This may leave a permanent twist in the
O-ring and reduce its effectiveness and shorten
its life.
When installing an O-ring, take extreme
care to avoid forcing it over sharp edges,
corners, and threaded sections. You should use
some type of sleeve or cover to avoid damaging
the O-ring.
FASTENERS
The proper use of fasteners is very important
and cannot be overemphasized. Many shipboard
machinery casualties have resulted from fasteners
that were not properly installed. Machinery
vibration,
thermal expansion, and thermal
contraction will loosen the fasteners. At sea,
loosening effects are increased by the pitch and
roll of the ship. You are familiar with such
standard fasteners as nuts, bolts, washers,
wingnuts, and screws. In this section we will
discuss some of the new developments in fastener
technology, such as the various types of locknuts,
which you may not be familiar with.
THREADED LOCKING DEVICES
An important part of fastener technology has
included the development of several methods for
locking mated threads of fasteners. Many of the
latest methods include the locking device or
method as an integral part of the fastener
assembly and are referred to as self-locking
nuts or bolts. Self-locking fasteners are more
expensive than some older methods but compare
favorably in cost with pin or wiring methods.
Length of Protrusion
Male threads on threaded fasteners, when
installed and tightened, will protrude the distance
of at least one thread length beyond the
top of the nut or plastic locking ring. Excessive
protrusion is a hazard, particularly where
necessary clearances, accessibility, and safety are
important. Where practicable, the number of
threads protruding should not exceed five. In no
case should thread protrusion exceed 10 threads
unless specifically approved by the work super-
visor. (This is the 1-to-10 rule.)
Where screw threads are used for setting or
adjusting (such as valve stem packing glands and
travel stops) or where installed threaded fasteners
do not strictly follow the 1-to-10 rule but have
given satisfactory service, the rule does not
apply. An example of an acceptable existing
installation would be where a male thread is flush
with the top of a nut or where more than 10
threads protruding is of no foreseeable con-
sequence.
Repair of Damaged Threads
You can remedy damaged external threads by
replacing the fastener. In large equipment castings
you must repair damaged internal threads to save
the part. You can repair internal threads by
redrilling the damaged thread; clean and either
install a solid wall insert or tap for a helical coil
insert. These inserts, in effect, return the tapped
hole to its original size so it takes the original
mating fastener.
LOCKNUTS
Locknuts are used in special applications
where you want to ensure that the components
joined by the fasteners will not loosen. Two types
of locknuts are in common use. The first type
applies pressure to the bolt thread and can be
used where frequent removal may be required.
The second type deforms the bolt thread and is
used only where frequent removal is unnecessary.
The first type includes plastic ring nuts, nylon
insert nuts, jam nuts, spring nuts, and spring
beam nuts. The second type includes distorted
collar nuts and distorted thread nuts; they are not
commonly found in gas turbine equipment and
will not be covered in this section.
9-45
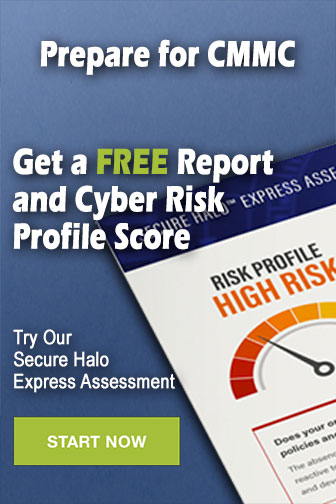