RELIEF VALVES. Relief valves are
automatic valves used on system lines and
equipment to prevent overpressurization. Most
relief valves simply lift (open) at a preset pressure
and reset (shut) when the pressure drops only
slightly below the lifting pressure. Figure 9-24
shows a relief valve of this type. System pressure
simply acts under the valve disk at the inlet of the
valve. When system pressure exceeds the force ex-
erted by the valve spring, the valve disk lifts off
its seat, allowing some of the system fluid to
escape through the valve outlet until system
pressure is reduced to just below the relief set
point of the valve. The spring then reseats the
valve. An operating lever is provided to allow
manual cycling of the relief valve or to gag it open
for certain tests. Virtually all relief valves are
provided with some type of device to allow
manual cycling.
Other types of relief valves are the high-
pressure air safety relief valve and the bleed air
surge relief valve. Both of these types of valves
are designed to open completely at a specified lift
pressure and to remain open until a specific reset
pressure is reachedat which time they shut.
Many different designs of these valves are used,
but the same result is achieved.
Figure 9-25.Pressure-reducing (spring-loaded) valve.
SPRING-LOADED REDUCING VALVES.
Spring-loaded reducing valves, one type of which
is shown in figure 9-25, are used in a wide variety
of applications. Low-pressure air reducers and
others are of this type. The valve simply uses
spring pressure against a diaphragm to open the
valve. On the bottom of the diaphragm, the outlet
pressure (the pressure in the reduced pressure
system) of the valve forces the disk upward to shut
the valve. When the outlet pressure drops below
the set point of the valve, the spring pressure
overcomes the outlet pressure and forces the valve
stem downward, opening the valve. As the outlet
pressure increases, approaching the desired value,
the pressure under the diaphragm begins to
overcome spring pressure, forcing the valve stem
upwards, shutting the valve. You can adjust the
downstream pressure by removing the valve cap
and turning the adjusting screw, which varies the
spring pressure against the diaphragm. This
particular spring-loaded valve will fail in the open
position if a diaphragm rupture occurs.
REMOTE-OPERATING VALVES. Remote-
operating gear is installed to provide a means of
operating certain valves from distant stations.
Remote-operating gear may be mechanical, hy-
draulic, pneumatic, or electric.
Some remote-operating gear for valves is used
in the normal operation of valves. For example,
the main drain system manual valves are opened
and closed by a reach rod or a series of reach rods
and gears. Reach rods may be used to operate
engine-room valves in instances where the valves
are difficult to reach from the operating stations.
Other remote-operating gear is installed as
emergency equipment. Some of the main drain
and almost all of the secondary drain system
valves are equipped with remote-operating gears.
You can operate these valves locally, or in an
emergency, you can operate them from remote
stations. Remote-operating gear also includes a
valve position indicator to show whether the valve
is open or closed.
PRESSURE-REDUCING VALVES. Pressure-
reducing valves are automatic valves that provide
a steady pressure into a system that is at a lower
pressure than the supply system. Reducing valves
of one type or another are found, for example,
in firemain, seawater, and other systems. A
reducing valve can normally be set for any desired
downstream pressure within the design limits of
the valve. Once the valve is set, the reduced
pressure will be maintained regardless of changes
9-17
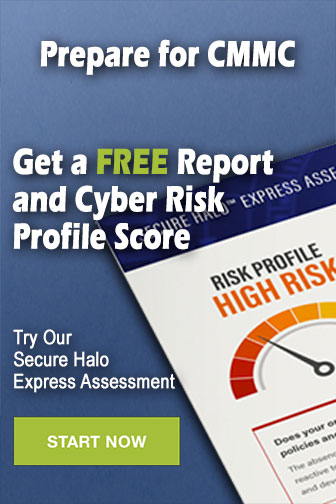