temperature of the available cooling medium, the only
way to make the vapor condense is to compress it.
When we raise the pressure, we also raise the
temperature. Therefore, we have raised its condensing
temperature, which allows us to use seawater as a
cooling medium in the condenser. In addition to this
primary function, the compressor also keeps the
refrigerant circulating and maintains the required
pressure difference between the high-pressure and
low-pressure sides of the system.
Many different types of compressors are used in
refrigeration systems. The designs of compressors vary
depending on the application of the refrigerants used in
the system. Figure 10-5 shows a motor-driven,
single-acting, two-cylinder, reciprocating compressor,
such as those commonly used in naval refrigeration
plants.
Compressors used in R-12 systems may be
lubricated either by splash lubrication or by pressure
lubrication. Splash lubrication, which depends on
maintaining a fairly high oil level in the compressor
crankcase, is usually satisfactory for smaller
compressors.
High-speed or large-capacity
compressors use pressure lubrications systems.
Capacity Control System
Most compressors are equipped with an
oil-pressure-operated automatic capacity control
system. This system unloads or cuts cylinders out of
operation following decreases in the refrigerant load
requirements of the plant. A cylinder is unloaded by a
mechanism that holds the suction valve open so that no
gas can be compressed.
Since oil pressure is required to load or put cylinders
into operation, the compressor will start with all
controlled cylinders unloaded. But as soon as the
compressor comes up to speed and full oil pressure is
developed, all cylinders will become operative. After
Figure 10-5.-Reciprocating compressor.
10-6
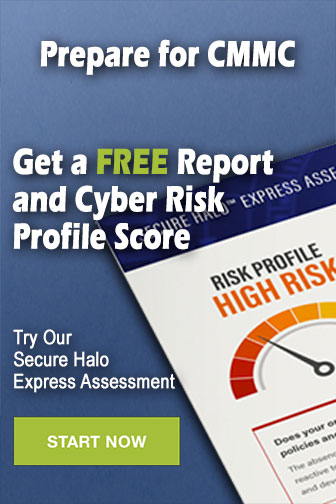