Figure 7-11.Electric starting system.
charging the battery with an engine-driven
generator.
The main components of the electric starting
system, as shown in figure 7-11, are the battery,
cranking motor, and associated control and
protective devices.
Electric Starting Systems
The starting motor for diesel and gasoline
engines operates on the same principle as a direct
current electric motor. The motor is designed to
carry extremely heavy loads but, because it draws
a high current (300 to 665 amperes), it tends to
overheat quickly. To avoid overheating, NEVER
allow the motor to run more than the specified
amount of time, usually 30 seconds at a time.
Then allow it to cool for 2 or 3 minutes before
using it again.
To start a diesel engine, you must turn it over
rapidly to obtain sufficient heat to ignite the fuel.
The starting motor is located near the flywheel,
and the drive gear on the starter is arranged so
that it can mesh with the teeth on the flywheel
when the starting switch is closed. The drive
mechanism must function to (1) transmit the
turning power to the engine when the starting
motor runs, (2) disconnect the starting motor
from the engine immediately after the engine has
started, and (3) provide a gear reduction ratio
between the starting motor and the engine.
The drive mechanism must disengage the
pinion from the flywheel immediately after
the engine starts. After the engine starts, its
speed may increase rapidly to approximately
1,500 rpm. If the drive pinion remained meshed
with the flywheel and also locked with the shaft
of the starting motor at a normal engine speed
(1,500 rpm), the shaft would be spun at a rapid
rate (22,500 to 30,000 rpm). At such speeds, the
starting motor would be badly damaged.
Hydraulic Starting Systems
There are several types of hydraulic starting
systems in use. In most installations, the system
consists of a hydraulic starting motor, a piston-
type accumulator, a manually operated hydraulic
pump, an engine-driven hydraulic pump, and a
reservoir for the hydraulic fluid.
Hydraulic pressure is provided in the accumu-
lator by the manually operated hand pump or
from the engine-driven pump when the engine is
operating.
When the starting lever is operated, the
control valve allows hydraulic oil (under pressure
of nitrogen gas) from the accumulator to pass
through the hydraulic starting motor, thereby
cranking the engine. When the starting lever is
released, spring action disengages the starting
pinion and closes the control valve. This stops the
flow of hydraulic oil from the accumulator. The
starter is protected from the high speeds of the
engine by the action of an overrunning clutch.
The hydraulic starting system is used on
some smaller diesel engines. This system can
be applied to most engines now in service without
modification.
Air Starting Systems
Starting air comes directly from the ships
medium-pressure (MP) or high-pressure (HP) air
service line or from the starting air flasks which
are included in some systems for the purpose of
storing starting air. From either source, the air,
7-12
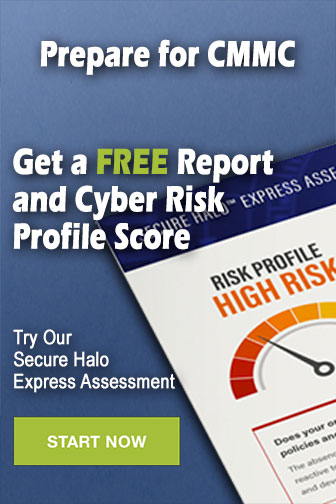