When the injector plunger is depressed, a fine
spray of fuel is discharged into the cylinder
through small holes in the nozzle. The smooth
operation of the engine depends, to a large
extent, on the accuracy with which the plungers
inject the same amount of fuel into every
cylinder.
The amount of fuel injected into the cylinders
on each stroke is controlled by rotating the
plungers of a unit injector. The throttle, which
regulates the speed of the engine, is connected to
the injectors through a suitable linkage. A change
in the throttle setting rotates the plungers and
varies the amount of fuel injected into the
cylinders on each stroke.
LUBRICATION SYSTEM
The lubrication system of an internal-combus-
tion engine is very important. If the lubricating
system should fail, not only will the engine stop,
but many of the parts are likely to be damaged
beyond repair. Therefore, when lubrication failure
occurs, the engine can seldom be run again
without a major overhaul.
The lubricating system delivers oil to the
moving parts of the engine to reduce friction and
to assist in keeping the parts cool. Most diesel and
gasoline engines are equipped with a pressure
lubricating system that delivers the oil under
pressure to the bearings and bushings and also
lubricates the gears and cylinder walls. The oil
usually reaches the bearings through passages
drilled in the framework of the engine. The
lubricating system of a typical diesel engine is
shown in figure 7-10.
All of the engine parts are lubricated with oil
delivered by a gear-type oil pump. This pump
takes suction through a screen from an oil pan
or sump. From the pump, the oil is forced through
the oil filter and the oil cooler into the main oil
gallery. The oil is fed from the main gallery,
through individual passages, to the main crank-
shaft bearings and one end of the hollow
camshaft. All the other moving parts and
bearings are lubricated by oil drawn from these
two sources. The cylinder walls and the teeth of
many of the gears are lubricated by oil spray
thrown off by the rotating crankshaft. After the
oil has served its purpose, it drains back to the
sump to be used again.
The oil pressure in the line leading from the
pump to the engine is indicated on a pressure
gauge. A temperature gauge in the return line
provides an indirect method for indicating
variations in the temperature of the engine parts.
Any abnormal drop in pressure or rise in
temperature should be investigated at once. It is
advisable to secure (shut down) the engine until
the trouble has been located and corrected.
Constant oil pressure, throughout a wide
range of engine speeds, is maintained by the oil
pressure relief valve that allows the excess oil to
flow back into the sump. All of the oil from the
pump passes through the filter unless the oil is
cold and heavy or if the filter (or oil cooler) is
clogged. In such cases, the bypass valve (filter
bypass valve or cooler bypass valve) is forced
open; and the oil flows directly to the engine. Part
of the oil fed to the engine is returned through
the bypass filter, which removes flakes of metal,
carbon particles, and other impurities.
COOLING SYSTEM
Marine engines are equipped with a water-
cooling system to carry away the excess heat
produced in the engine cylinders. Fresh water
(coolant) is circulated through passages in the
cylinder walls and in the cylinder head, where it
becomes hot from absorbing engine heat. The hot
coolant then passes through a heat exchanger,
where it gives up its heat to a cooling medium,
becomes cool, and returns to the engine to remove
more heat. The cooling medium may be either air
or seawater.
A heat exchanger using air as the cooling
medium works like an automobile radiator. A
heat exchanger using seawater as the cooling
medium may be mounted either on the engine
or on the ships hull. Engine-mounted heat
exchangers require seawater to be pumped to
and from them; whereas, hull-mounted heat
exchangers (keel coolers) are in constant contact
with seawater and require the fresh water (coolant)
to be pumped through the cooler.
STARTING SYSTEMS
There are three types of starting systems used
in internal-combustion engineselectric,
hydraulic, and compressed air.
As a Fireman, you will probably have more
contact with the electric starting system than you
will with the other two types. Lifeboats aboard
ships use an electric starter to start the engine.
Electric starting systems use direct current
because electrical energy in this form can be stored
in batteries and drawn upon when needed. The
batterys electrical energy can be restored by
7-11
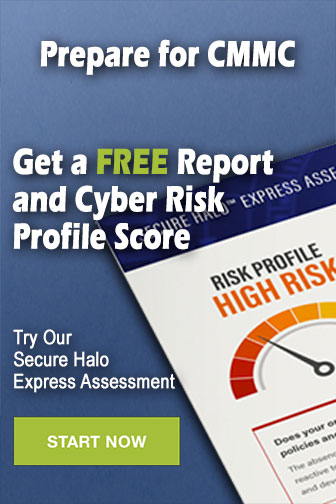