. The light-off and securing schedules were
prepared by each ship and were not
standardized between ships. The schedules
were written for general, rather than
specific, equipment or systems. They did
not include alternatives between all the
existing modes of operation.
Following these studies, NAVSEA developed
the EOSS. It is designed to help eliminate
operational problems. The EOSS involves the
participation of all personnel from the department
head to the watch stander. The EOSS is a set of
systematic and detailed written procedures. The
EOSS uses charts, instructions, and diagrams
developed specifically for the operational and
casualty control function of a specific ships
engineering plant.
The EOSS is designed to improve the
operational readiness of the ships engineering
plant. It does this by increasing its operational
efficiency and providing better engineering plant
control. It also reduces operational casualties and
extends the equipment life. These objectives are
accomplished first by defining the levels of
control; second, by operating within the engineer-
ing plant guidelines; and last, by providing each
supervisor and operator with the information
needed. This is done by putting these objectives
in words they can understand at their watch
station.
The EOSS is composed of three basic parts.
l The Users Guide
. The engineering operational procedures
(EOP)
. The engineering operational casualty con-
trol (EOCC)
EOSS USERS GUIDE
The Users Guide is a booklet that explains
the EOSS package and how to use it to the
ships best advantage. It has document samples
and explains how they are used. It provides
recommendations for training the ships person-
nel using the specified procedures.
The EOSS documentation is developed using
work-study techniques. All existing methods and
procedures for plant operation and casualty
control procedures are documented. These include
the actual ship procedures as well as those pro-
cedures contained in available reference sources.
Each action is subjected to a serious review
to measure the completeness of the present
methods. At the completion of this analytic phase,
new procedural steps are developed into an
operational sequencing system. Step-by-step,
time-sequenced procedures and configuration
diagrams are prepared to show the plant layout
in relation to operational components. The final
step in the development phase of an EOSS is a
validation on board ship. This is done to verify
technical accuracy and adequacy of the prepared
sequencing system. All required corrections are
made. They are then incorporated into the
package before installation aboard ship.
The resulting sequencing system provides the
best tailored operating and casualty control
procedures available that apply to a particular
ships propulsion plant. Each level is designed
with the information required to enable the
engineering plant to respond to any demands
placed upon it.
ENGINEERING OPERATIONAL
PROCEDURES
The EOP has all the information necessary for
the proper operation of a ships engineering plant.
It has guides for scheduling, controlling, and
directing plant evolutions through operational
modes. This includes receiving shore services, to
various modes of in-port auxiliary plant steaming,
to underway steaming.
The EOP documentation exists for specifically
defined operational stages. These are defined as
stages I, II, and III.
Stage I deals with the total engineering plant
under the direct responsibility of the plant
supervisor (EOOW). The EOOW coordinates the
placing in operation and securing of all systems
and components normally controlled by the
various space supervisors. This person also
supervises those functions that affect conditions
internal to the engineering plant, such as jacking,
testing, and spinning main engines. The EOP
documentation helps the plant supervisor
guarantee optimum plant operating efficiency,
proper sequencing of events in each evolution, and
the training of newly assigned personnel. During
a plant evolution, the EOOW appoints control
and operation of the following systems and
components:
. Systems that interconnect one or more
engineering plant machinery spaces and
electrical systems.
1-13
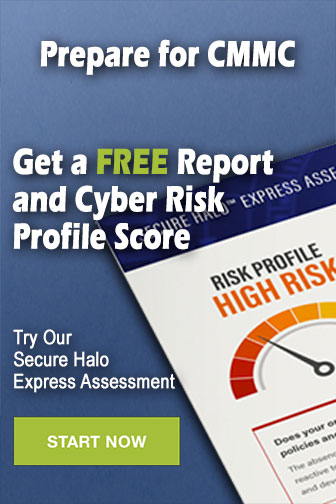