not reach electrical machinery or wiring; and
(3) ensuring that safety guards are provided at
potential danger points, such as rotating and
reciprocating equipment.
For personnel and machinery safety, you must
adhere to the following safety precautions
specifically related to the engineering department:
Do not attempt to operate equipment
by overriding automatic shutdown or
warning devices.
Tag-out and disconnect batteries or other
sources of electrical power before per-
forming maintenance. This prevents
injuries from short circuits and accidental
start-up of equipment.
Avoid holding or touching spark plugs,
ignition units, or high-tension leads while
they are energized.
Do not use oxygen to pressure test fuel
lines and equipment.
Take precautions to avoid inhaling vapors
of lacquer thinner, trichlorethylene, and
similar solvents.
Do not wear jewelry or watches while
working in machinery spaces.
Take precautions to avoid touching
exposed hot parts of an engine. Do not
perform maintenance work until the engine
has been shut down and cooled.
Wear proper ear protection in all main
machinery spaces.
It is the responsibility of supervisory personnel
to ensure that their subordinates are instructed in
and carry out the applicable safety precautions.
Each individual is responsible for knowing and
observing all safety precautions applicable to their
living or working spaces. Refer to Navy Safety
Precautions for Forces Afloat, OPNAVINST
5100.19.
SHIPS MAINTENANCE AND
MATERIAL MANAGEMENT
(3-M) SYSTEMS
The Ships Maintenance and Material Manage-
ment (3-M) Manual, OPNAVINST 4790.4,
describes in detail the Ships 3-M Systems. The
primary objective of the Ships 3-M Systems is
to provide for managing maintenance and mainte-
nance support in a way to ensure maximum
equipment operational readiness. The Ships 3-M
Systems is divided into two subsystems. They are
the planned maintenance system (PMS) and the
maintenance data system (MDS).
PURPOSES OF PMS
The PMS was established for the following
purposes:
To reduce complex maintenance to sim-
plified procedures that are easily identified
and managed at all levels
To define the minimum planned mainte-
nance required to schedule and control
PMS performances
To describe the methods and tools to be
used
To provide for the detection and prevention
of impending casualties
To forecast and plan personnel and
material requirements
To plan and schedule maintenance tasks
To estimate and evaluate material
readiness
To detect areas requiring additional or
improved personnel training and/or
improved maintenance techniques or
attention
To provide increased readiness of the ship
BENEFITS OF PMS
The PMS is a tool of command. By using
PMS, the commanding officer can readily
determine whether the ship is being properly
maintained. Reliability and availability are
improved. Preventive maintenance reduces the
need for major corrective maintenance, increases
economy, and saves the cost of repairs.
The PMS assures better records because the
shipboard maintenance manager has more useful
data. The flexibility of the system allows for
programming of inevitable changes in employ-
ment schedules. This helps to better plan
preventive maintenance.
1-9
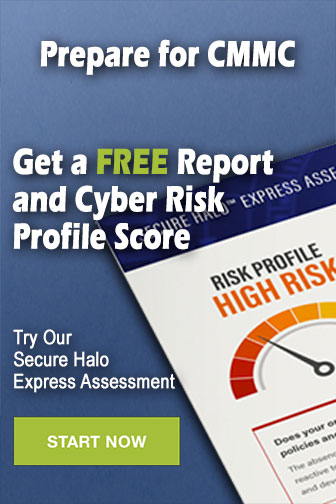