both valves are operated together. This allows rapid
shifting from the on-service pumping unit to the standby
unit; it prevents lining up both pumps to the ram at the
same time. The hand lever is usually located between
the trick wheels. It has three positions marked P, N, and
S. P denotes the port pump is connected to the ram; N
denotes neutral (neither pump connected to the ram);
and S denotes the starboard pump is connected to the
ram. Also, the hand lever is usually connected to motor
switches. This lets the operator connect the selected
pump to the ram and start the pump drive motor in one
quick operation. In most ships this valve is electrically
controlled by the motor controller and by pressure
switches.
Principles of Operation
The on-service hydraulic pump is running at all
times and is a constant-speed pump. Unless steering is
actually taking place, the tilt box of the main hydraulic
pump is at zero stroke, and no oil is being moved within
the main system. The auxiliary pump provides control
oil and supercharge flows for the system.
To understand the operation of the pump, lets
assume that a steering order signal comes into the
differential control box. It can come from either the
remote steering system in the ships wheelhouse or the
trick wheel. The control box mechanically positions the
tilt box of the main hydraulic pump to the required angle
and position.
NOTE: Remember that direction of fluid and flow
may be in either direction in a hydraulic speed gear. It
depends on which way the tilt box is angled. For this
reason, the constant-speed, unidirectional motor can be
used to drive the main hydraulic pump. The pump will
still have the capability to drive the ram in either
direction.
With the main hydraulic pump now pumping fluid
into one of the ram cylinders, the ram moves, moving
the rudders. A rack and gear are attached to the rudder
yoke between the rudder links. As the ram and the rudder
move, the rack gear moves, driving the follow-up pinion
gear. The pinions drive follow-up shafts that feed into
the differential box. This feedback or servo system tells
the differential control box when the steering operation
is complete. As the ordered rudder angle is approached,
the differential control box begins realigning the tilt box
of the main hydraulic pump. By the time the desired
rudder angle is reached, the tilt box is at zero stroke. This
means that the ordered signal (from the pilot house or
trick wheel) and the actual signal (from the follow-up
shafts) are the same. If either of these change, the
differential control box reacts accordingly; the main
hydraulic unit pumps oil to one end or the other of the
ram.
The trick wheels provide local-hydraulic control of
the steering system of the remote steering system fails.
A hand pump and associated service lines are also
provided for local-manual operation of the ram if both
hydraulic pump units fail.
Operation and Maintenance
The Machinists Mate watch stander usually
operates the steering equipment only in abnormal and
emergency situations. For this reason, you should be
thoroughly familiar with all emergency procedures,
such as local-hydraulic steering with the trick wheel and
local-manual steering with the hand pump. Operating
instructions and system diagrams are normally posted
near the steering gear. The diagrams describe the various
procedures and lineups for operation of the steering
gear. Be sure that the standby equipment is ready for
instant use.
General maintenance of the steering gear requires
that you clean, inspect, and lubricate the mechanical
parts and maintain the hydraulic oil at the proper level
and purity. The Planned Maintenance System (PMS)
lists the individual requirements for the equipment. The
electricians maintain the electrical portion of the
steering system, including the control system.
ANCHOR WINDLASSES
In a typical electrohydraulic mechanism, one
constant-speed electric motor drives two
variable-stroke pumps through a coupling and reduction
gear. Other installations include two motors, one for
driving each pump. Each pump normally drives one
wildcat. However, if you use a three-way plug cock-type
valve, either pump may drive either of the two wildcats.
The hydraulic motors drive the wildcat shafts with a
multiple-spur gearing and a locking head. The locking
head allows you to disconnect the wildcat shaft and
permits free operation of the wildcat, as when dropping
anchor.
Each windlass pump is controlled either from the
weather deck or locally. The controls are handwheels on
shafting that lead to the pump control. The hydraulic
system requires your attention. Make sure the hydraulic
system is always serviced with the specified type of
clean oil.
10-43
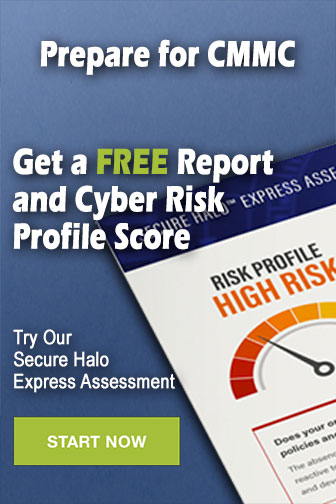