Electrohydraulic equipment for the crane consists
of one or more electric motors running at constant speed.
E a c h m o t o r d r i v e s o n e o r m o r e A - e nd
variable-displacement hydraulic pumps. The pump
strokes are controlled through operating handwheels.
START, STOP, and EMERGENCY RUN pushbuttons
at the operators station control the electric motors.
Interlocks prevent starting the electric motors when the
hydraulic pumps are on stroke. B-end hydraulic motors
are connected to the A-end pumps by piping. They drive
the drums of the hoisting and topping units or the
rotating machinery.
Reduction gears are located between the electric
motor and the A-end pump and between the B-end
hydraulic motor and the rotating pinion. Each hoisting,
topping, and rotating drive has an electric brake on the
hydraulic motor output shaft. This brake is interlocked
with the hydraulic pump control. It will set when the
hydraulic control is on neutral or when electric power is
lost. A centering device is used to find and retain the
neutral position of the hydraulic pump.
Relief valves protect the hydraulic system. These
valves are set according to the requirements of chapter
556 of the NSTM.
Cranes usually have a rapid slack take-up device
consisting of an electric torque motor. This motor is
connected to the hoist drum through reduction gearing.
This device works in conjunction with the pressure
stroke control on the hydraulic pump. It provides fast
acceleration of the hook in the hoisting direction under
light hook conditions. Thus, slack in the cable is
prevented when hoisting is started.
Some cranes have a light-hook paying-out device
mounted on the end of the boom. It pays out the heisting
cables when the weight of the hook and cable beyond
the boom-head sheave is insufficient to overhaul the
cable as fast as it is unreeled from the hoisting drum.
When the mechanical hoist control is in neutral, the
torque motor is not energized and the cable is gripped
lightly by the action of a spring. Moving the hoist control
to LOWER energizes the torque motor. The sheaves
clamp and pay out the cable as it is unreeled from the
hoist drum. When the hoist control is moved to HOIST,
the torque motor is reversed and unclamps the sheaves.
Alimit switch opens and automatically de-energizes the
paying-out device.
Maintain cranes according to the PMS requirements
or the manufactured instructions. Keep the oil in the
replenishing tanks at the prescribed levels. Keep the
system clean and free of air. Check the limit stop and
other mechanical safety devices regularly for proper
operation. When cranes are not in use, secure them in
their stowed positions. Secure all electric power to the
controllers.
ELECTROHYDRAULIC ELEVATORS
Some of the hydraulic equipment that you maintain
is found in electrohydraulic elevator installations.
Modern carriers use elevators of this type. The elevators
described in this chapter are now in service in some of
the ships of the CV class. These ships are equipped with
four, deck-edge airplane elevators having a maximum
lift capacity of 79,000 to 105,000 pounds. The cable lift
platform of each elevator projects over the side of the
ship and is operated by an electrohydraulic plant.
Electrohydraulic Power Plant
The electrohydraulic power plant for the elevators
consists of the following components:
1.
2.
3.
4.
5.
6.
7.
8.
9.
A horizontal plunger-type hydraulic engine
Multiple variable-delivery parallel piston-type
pumps
Two high-pressure tanks
One low-pressure tank
A sump tank system
Two constant-delivery vane-type pumps (sump
pumps)
An oil storage tank
A piping system and valves
A nitrogen supply
The hydraulic engine is operated by pressure
developed in a closed hydraulic system. Oil is supplied
to the system in sufficient quantity to cover the baffle
plates in the high-pressure tanks and allow for piston
displacement. Nitrogen is used because air and oil in
contact under high pressure form an explosive mixture.
Air should not be used except in an emergency.
Nitrogen, when used, should be kept at 97 percent purity.
The hydraulic engine has a balanced piston-type
valve with control orifices and a differential control unit.
This control assembly is actuated by an electric motor
and can be operated by hand. To raise the elevator, move
the valve off center to allow high-pressure oil to enter
the cylinder. High-pressure oil entering the cylinder
moves the ram. The ram works through a system of
cables and sheaves to move the platform upward. The
10-47
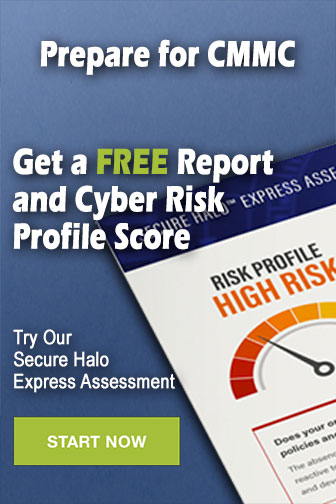