speed of the elevator is controlled by the amount of
pressure in the high-pressure tank and the control valve.
When the elevator starts upward, the pressure in the
high-pressure tank drops. The pressure drop
automatically starts the main pumps. These pumps
transfer oil from the low-pressure tank to the
high-pressure system until the pressure is restored. An
electrical stopping device automatically limits the
stroke of the ram and stops the platform at the proper
position at the flight deck level.
To lower the elevator, move the control valve in the
opposite direction. This lets oil in the cylinder flow into
the exhaust tank. As the platform descends, oil is
discharged to the low-pressure tank (exhaust tank). The
original oil levels and pressures, except for leaks, are
reestablished. The lowering speed is controlled by the
control valve and the cushioning effect of the pressure
in the exhaust tank. Leak is drained to the sump tanks.
It is then automatically transferred to the pressure
system by the sump pumps. An electrically operated
stopping device automatically slows down the ram and
stops the platform at its lower level (hangar deck).
Safety Features
The following list contains some of the major safety
features incorporated into modem deck-edge elevators:
1. If the electrical power fails while the platform is
at the hangar deck, there will be enough pressure in the
system to move the platform to the flight deck one time
without the pumps running.
2. Some platforms have serrated safety shoes. If all
the hoisting cable should break on one side, the shoes
will wedge the platform between the guide rails. This
will stop the platform with minimum damage.
3. A main pump may have a pressure-actuated
switch to stop the pump motors when the discharge
pressure is excessive. They may also have to relieve the
pressure when the pressure switch fails to operate.
4. The sump pump system has enough capacity to
return the unloaded platform from the hangar deck to
the flight deck.
5. The oil filter system maybe used continuously
while the engine is running. This allows part of the oil
to be cleaned with each operation of the elevater.
ELECTROMECHANICAL ELEVATORS
Electromechanical elevators are used for freight,
bombs, and stores. In this type of elevator, the platform
is raised and lowered by one or more wire ropes that
pass over pulleys and wind or unwind on hoisting
drums. Hoisting drums are driven through a reduction
gear unit by an electric motor. An electric brake stops
and holds the platform. The motor has two speeds, full
speed and low, or one-sixth, speed. Control
arrangements allow the elevator to start and run on high
speed. Low speed is used for automatic deceleration as
the elevator approaches the selected level. The platform
travels on two or four guides. Hand-operated or
power-operated lock bars, equipped with electrical
interlocks, hold the platform in position.
LUBRICATING SYSTEMS
Most equipment is provided with a lubricating
system that supplies oil under pressure to the bearings.
The system consists of a sump or reservoir for storing
the oil, an oil pump, a strainer, a cooler, temperature and
pressure gauges, and the necessary piping to carry the
oil to the bearings and back to the sump. The location
and arrangement of these parts vary with each piece of
equipment. This system allows the lube-oil system to
perform the following functions:
l Supply lubrication to the bearings
. Cool the bearings
. Flush any wear products from the bearings
The lube-oil pump is generally a gear-type pump. A
definite pressure is maintained in the oil feed lines. A
pressure relief valve allows excess oil to recirculate to
the suction side of the pump.
Quite often, dual strainers are connected in the line
so that the system can operate on one strainer while the
other one is being cleaned. The tube-in-shell type of
cooler is generally used with seawater circulating
through the tubes and the oil flowing around them. The
temperature of the oil is controlled by adjusting the
valve that regulates the amount of seawater flowing
through the tubes.
Oil must be supplied to the bearings at the
prescribed pressure and within certain temperature
limits. A pressure gauge installed in the feed line and a
thermometer installed in the return line indicate oil
system functioning. Thermometers are often installed in
the bearings to serve as a warning against overheating.
If there is a decided drop in oil pressure, shut down the
equipment immediately. You should investigate even a
moderate rise in the oil temperature. An oil-level float
gauge indicates the amount of oil in the sump. Some
bearings do not require a lot of cooling or flushing of
10-48
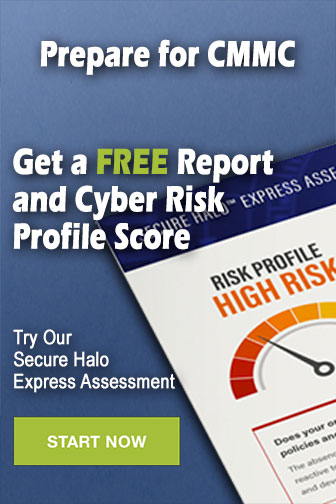